Pulverizer Vibration
(Rumbling)
Causes and Remedies for Pulverizer “Rumbling ” Associated with High Fineness Levels
The merits of improved pulverizer performance on combustion efficiency, NOx, flyash L.O.I., etc have been well documented earlier. Much of the improvement can be traced to the need to achieve higher fineness levels. As we have mentioned before, our goal for optimum combustion is to attain a minimum of >75% passing 200 Mesh with <0.5% remaining on the 50 Mesh at pulverizer full load. Higher fineness at full load can cause extremely high fineness at lower coal flows. In some instances in which pulverizer fineness has been achieved, higher fineness levels have caused certain pulverizers to “rumble”; especially at the lower pulverizer loads.
As pulverizer load is decreased and primary airflow decreases to maintain the proper air/fuel ratio, the velocities across the pulverizer throat also decrease. This causes less material to be evacuated from the pulverizer, thus remaining in the pulverizer for longer periods (increased re-circulation). The end result is that pulverizer fineness at the lower loads increases. On pulverizers with >75% passing 200
Mesh fineness at full load, minimum load fineness can be as high as 85% or more. |
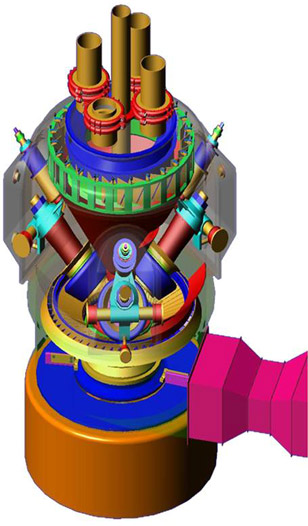 |
In some instances, an excessive quantity of finely ground coal particles on the bowl acts as a powder lubricant between the roll and bowl. The friction between the coal and grinding segments is not enough to overcome the roller bearing friction and the roll fails to turn, causing a “rumble”. This “rumble” in almost all cases is caused by very high fineness. There are two recommended courses of action to alleviate the “rumble”.
The first, and preferable, is simply to raise the minimum load point at which the pulverizer is removed from “service”. Higher coal flows will result in lower fineness.
The second, which is rarely needed, is to install small irregularities in the grinding ring that “bump” the roll and keep it turning. This can be accomplished with either vertical gouges or vertical weld-overlay ridges in the bowl. The number of ridges/gouges should be such that the total number is not devisable by the number of journals. In most cases, plants install (4) ridges/gouges 90° apart on the bowl. The reason is so that no more than (1) ridge/gouge is under a roll at a time to limit vibration. The first option of changing a pulverizers minimum load is preferred and more often than not, successful.
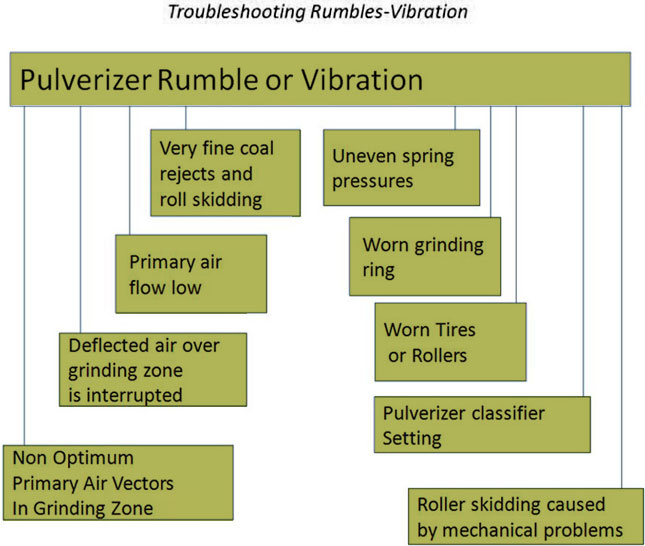